This discussion helps define the importance of maintaining ejection seat configuration and currency to ensure that, when required, the seat will provide the highest probability for a safe escape, and safe descent to the ground under a good parachute. A great amount of effort is put into design, development and qualification testing of an ejection seat system before it is put into service to ensure its reliability and safety. It is critical to maintain and use the ejection seat within the scope for which it was designed, assuring the highest level of reliability and safety. Reliability is dependent on the configuration of the seat, from the smallest screw, to the personal parachute system configuration, and the age of the pyrotechnic devices, the helmet, and harness the pilot is wearing. Changes to any aspect of the system increases the risk of a disastrous result when the handle is pulled. It is a system with every component being key to its success. This discussion is an attempt to describe the details of a qualified escape system and how important it is to maintain it as your last resort.
Design and Qualification
An ejection seat is typically designed to perform at aircraft speeds from 0 to 600 knots. Most are designed to work reliably with pilot weights between approximately 140 pounds and 220 pounds. The latest generation seats are designed to accommodate aircrew weights ranging from 103 pounds up to 245 pounds. Qualification of an ejection seat is based on:
- the performance of the airplane
- the weight of the aircrew
- the limited capabilities of the components and subsystems
- the aircrew ensemble
- the sequencing of events
Typically, qualification begins with individual testing of each component and subsystems followed by the testing of the full-up ejection seat system. The full-up escape system testing requires the successful completion of 22 sled tests where seats are ejected at different speeds and carrying different weights of occupants equipped with different flight equipment options. Through this process, the seat is qualified as a complete system, including:
- specific pyrotechnic (CAD/PAD) devices,
- specific parachute system, and
- specific aircrew flight equipment (helmet, mask, harness, etc.)
This extensive, detailed testing qualifies the SYSTEM to minimize risk and maximize the probability of a safe ejection. Any changes to a proven QUALIFIED system must be carefully evaluated by professionals and may require testing to ensure the continued reliability and safety of the system. Many variables effect the performance of an ejection seat – changes increase chances that things will go wrong.
Pyrotechnic Components, CAD/PAD
Some of the most important subcomponents of an ejection seat system are the Cartridge Actuated Devices and Propellant Actuates Devices. The military term is “CAD/PAD.” In most cases there are between 10 and 20 such devices performing varied tasks during an ejection sequence.
- A gas generator will “haul-back” the occupant into the seat just prior to ejection
- A pyrotechnic time delay provides correct sequencing of events such as canopy jettison or fracture, ejection seat initiation and safe separation of front and rear seats
- A CAD/PAD item will provide time delay sequencing of the Catapult and Rocket Motor that propels the ejection seat up and away from the aircraft
- A CAD/PAD item provides Drogue Parachute deployment or parachute spreading for quick-parachute deployment scenarios, such as low altitude ejections
- CAD/PAD items provide deployment of survival kit and locator beacon
- CAD/PAD items will delay parachute opening until a safe speed or altitude is reached
All CAD/PAD items have completed extensive qualification testing for its specific application. Each CAD/PAD item is made up of different constituents and each item is exposed to different environments during its life. Assigned life of each item is different. Life is assigned by an authority like the US Navy or the US Air Force (not by the manufacturer). Its assigned life is based on testing that shows where degradation of performance is seen during surveillance testing throughout the life of the CAD/PAD item. CAD/PAD items should not be used past their assigned life. Performance of the item has reduced reliability and may become hazardous.
It is very important to understand that these items are life-limited. A CAD/PAD device is not good forever. Each of these components has an assigned life based on real testing data and solid performance history data. CAD/PAD items will have a storage or “shelf” life, and an installed or “service” life (Shelf/Service Life). Life of an item can be as little as 2 years or as much as 15 years. Today’s modern CAD/PAD items are typically assigned lives of 5 to 10 years.
The constituents that make up the Energetic Materials (propellant, powder, etc.) of a CAD/PAD device are age-sensitive and are effected by temperature. These materials change properties and characteristics over time and temperature. Long-times and high-temperatures are the enemy of CAD/PAD items. It is important to store CAD/PAD items in cool storage magazines when not installed in the aircraft and to park airplanes under awnings or in hangars to minimize the effect of elevated temperatures resulting from sunlight exposure. Changes in CAD/PAD performance can range from slower performance to faster performance, to simply not functioning at all. The constituents are chemicals. Chemicals change over time and at different rates based on temperature. Materials change and may get more sensitive over time and exposure to temperatures. The change may result in the auto-ignition of the item.
In July of 2007 a PDRM (Parachute Deployment Rocket Motor) in the ejection seat of an aircraft sitting on the ramp at China Lake, California auto-ignited. The resulting explosion destroyed the canopy and severely damaged the ejection seat (photo below).
Fortunately, there was no one in the seat or near the airplane at the time. The subsequent investigation revealed that the Energetic Materials had consumed the stabilizer and the reaction heated the propellant to its auto-ignition temperature. Propellant decomposition is accelerated by exposure to high temperatures. This item was simply sitting in the airplane on the ramp, and went off.

Damage Resulting From PDRM Auto-Ignition
CAD/PAD items degrade in different ways. From lower gas pressure, to different times in a time delay, to auto-ignition as seen above.
CAD/PAD time delays that are expected to deliver a quarter second delay between canopy jettison and seat ejection, may become 3 seconds, or become immediate with change over time and temperature exposure. A time delay is a critical component with a qualified life expectancy. You cannot depend on CAD/PAD items after their assigned life has expired. The risk is too great.
As mentioned, CAD/PAD explosive constituents are chemicals. Much like a paint can stored in your garage for 15 years. You would not expect it to be the same paint when you try to paint something after 15 years of storage. Chemicals change. Things separate. It is the same with a CAD/PAD item.
Cloth/Fabric Items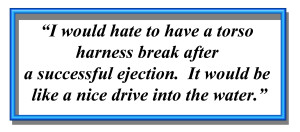
Other items of concern regarding shelf/service life, as well as time and temperature exposure are the fabric items. Fabric items such as harnesses, risers, lap belts, inertia reel straps, drogue chutes and personnel parachutes are all life limited like CAD/PAD items.They require periodic inspection and replacement when they reach their assigned life or when inspection reveals issues that could cause failure during an ejection. Failure of any of these items during an ejection could be disastrous. Qualified, trained personnel verify and maintain the performance of these critical items per specific specifications.
Ejection Seats
Ejection seats fly in aircraft under extreme environments like shock, vibration, temperature, humidity, salt/fog conditions and extreme g-levels. The ejection seat is expected to work when it is required, regardless of the environment it has lived within. An ejection seat is an amazingly efficient piece of safety equipment. An ejection seat has a maintenance schedule, like the aircraft, like your car, and is maintained per specific technical documentation by trained personnel. Typically there is a minor inspection at one year and a major inspection/ overhaul at 6 years. All seats are not the same though. See the applicable technical documentation. Corrosion or cracks can be found during inspections and are repaired or treated as required. Certified technicians familiar with the ejection seat and the nuances of particular ejection seats are required for correct maintenance. An ejection seat maintainer is trained specifically for that system, much like an engine maintainer is trained for that expertise.
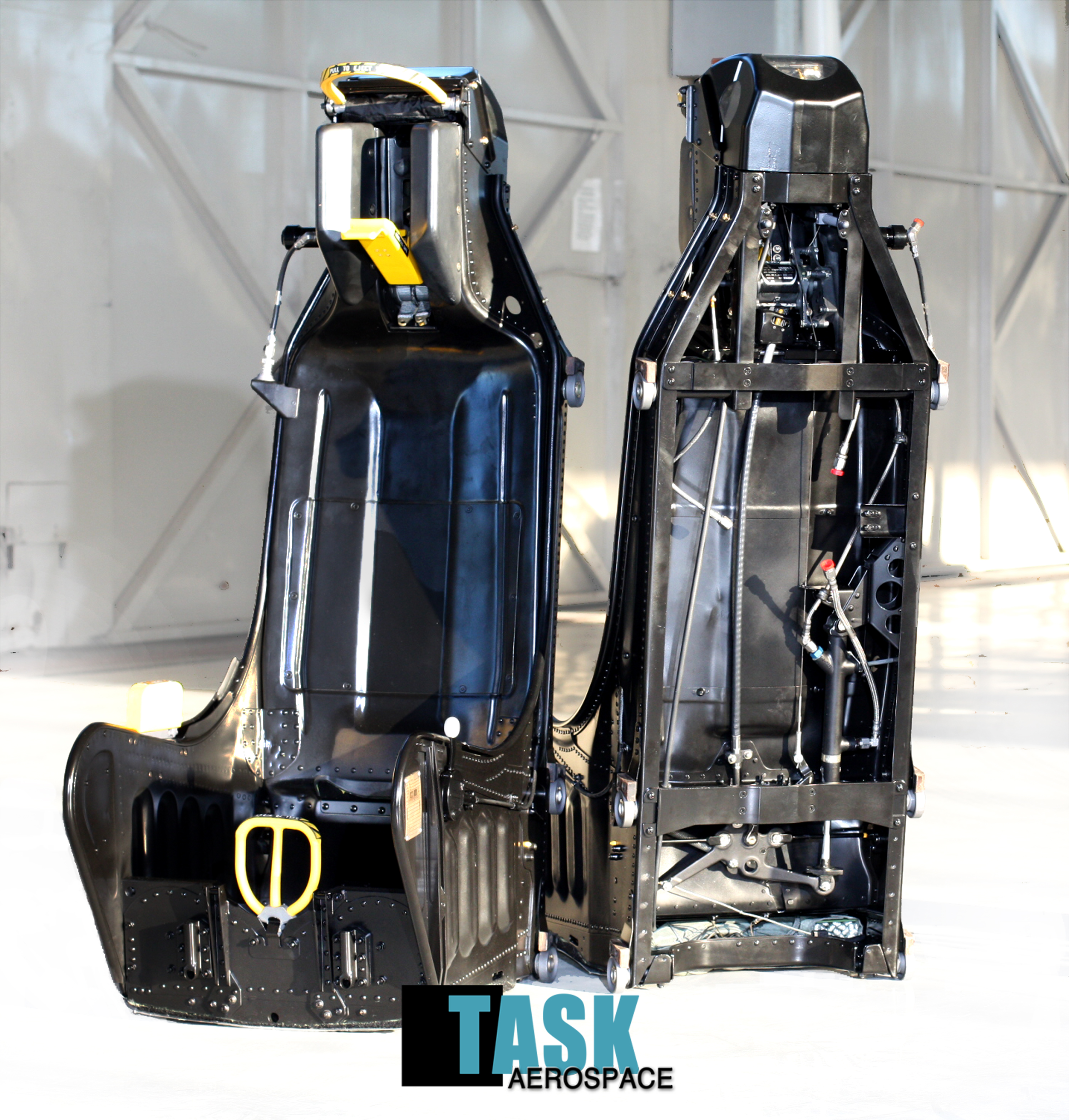
F-16 Aircraft, ACES II® Ejection Seat. Successful Ejection!
ACES II® is a Registered Trademark of Collins Aerospace
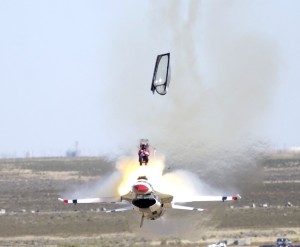
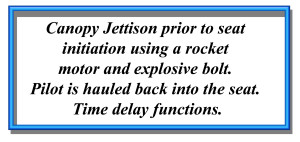
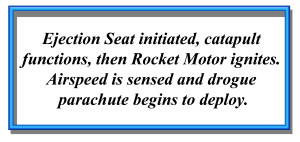
Summarizing
In summary, it is imperative that the entire escape system be:
- Operated and maintained in accordance with applicable technical documentation and the aircraft manufacturer’s instructions
- Equipped with serviceable, qualified, time-life compliant components
Failure to do so can result in serious injuries or even fatalities.
If you have questions regarding your escape system, whether it is the seat, the aircraft mounted equipment, the aircrew flight equipment, or the CAD/PAD items, let Task take a look to be certain you are operating at the highest level of safety. Task can locate hard to find items and looks forward to hearing from you.